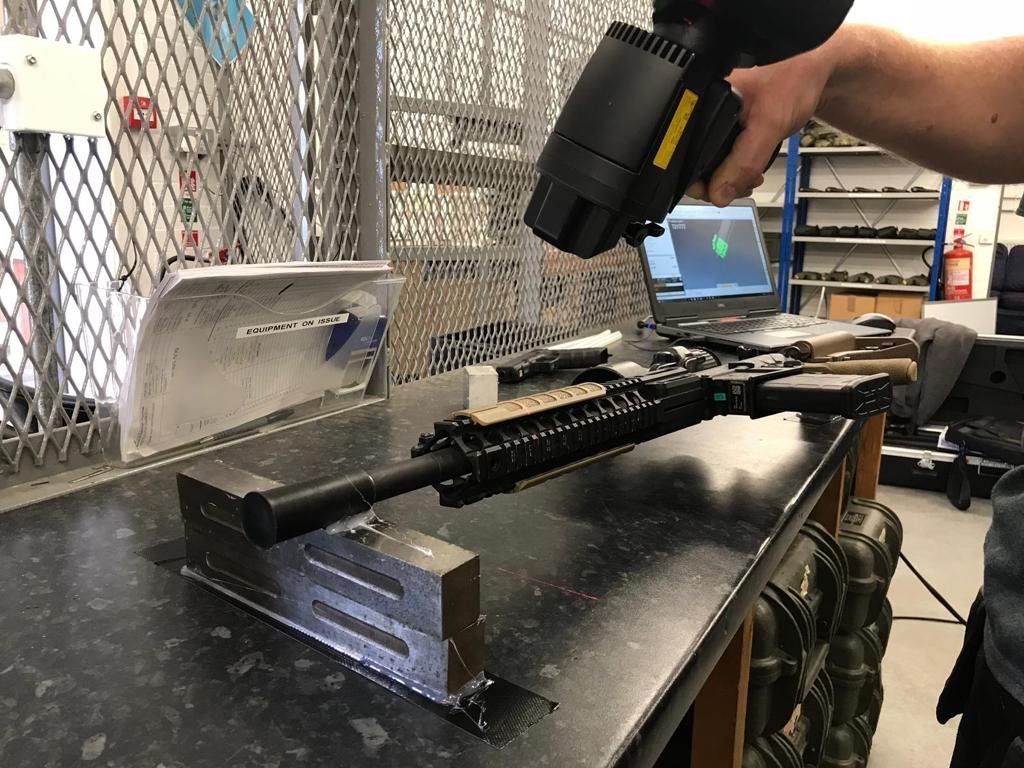
Unlocking innovation with reverse engineering techniques
Reverse engineering offers valuable insights and opportunities for advancement. This process is highly beneficial for innovation in sectors involving manufacturing and design.
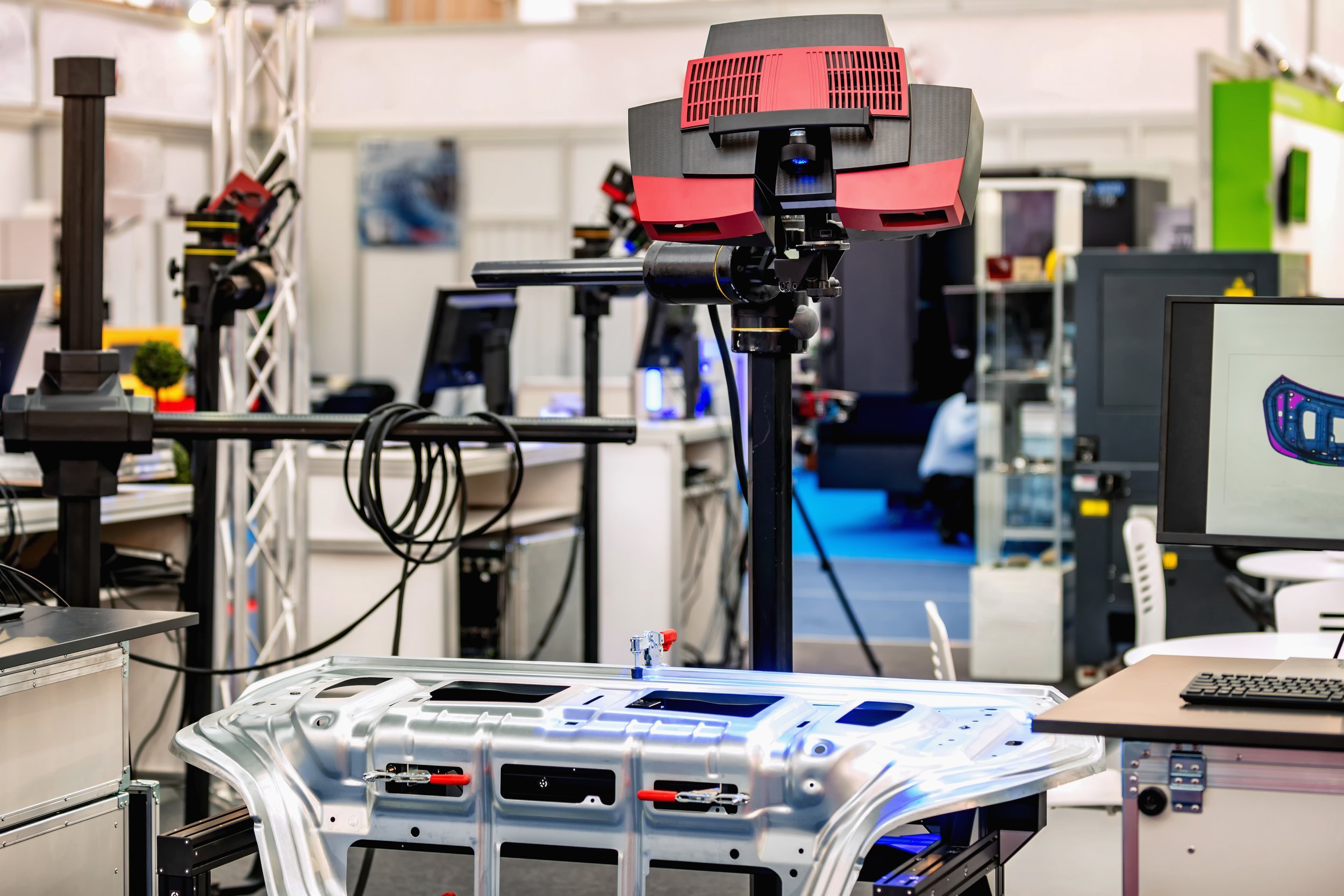
How component verification can prevent costly manufacturing errors
In modern manufacturing, precision is not just desirable; it’s essential. Each component within an assembly plays a critical role in ensuring the functionality, safety, and quality of the final product. Even the smallest imperfection in a part can cascade into significant problems, from operational inefficiencies to product recalls.
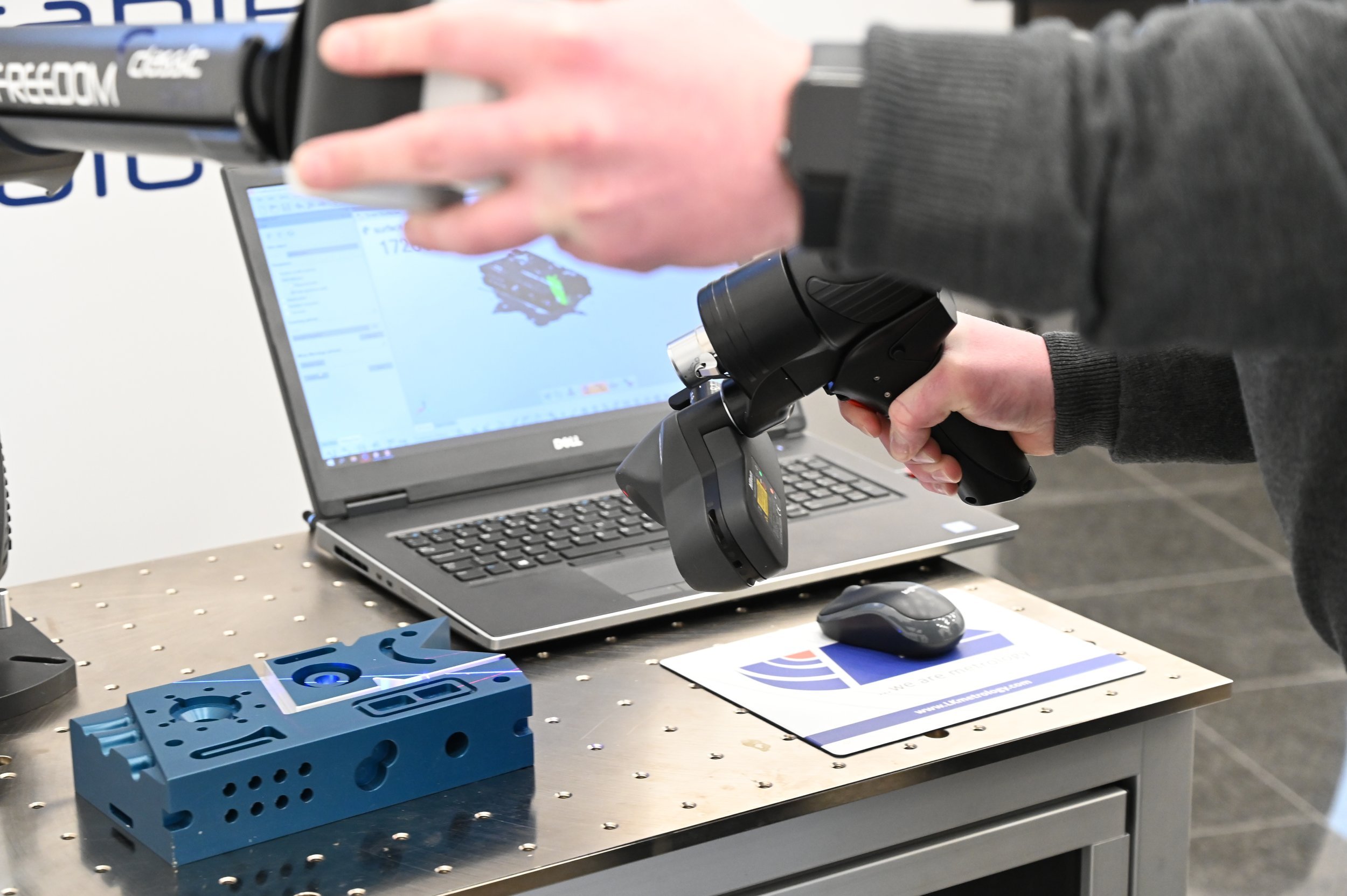
Why regular calibration and recertification are crucial for quality control
In precision manufacturing, quality control is a core component of maintaining product integrity and consistency. At the heart of effective quality control lies the accuracy of measurement tools and systems. These tools, whether used in measurement or other forms of dimensional analysis, must repeatedly deliver precise results to ensure every product meets exact specifications.
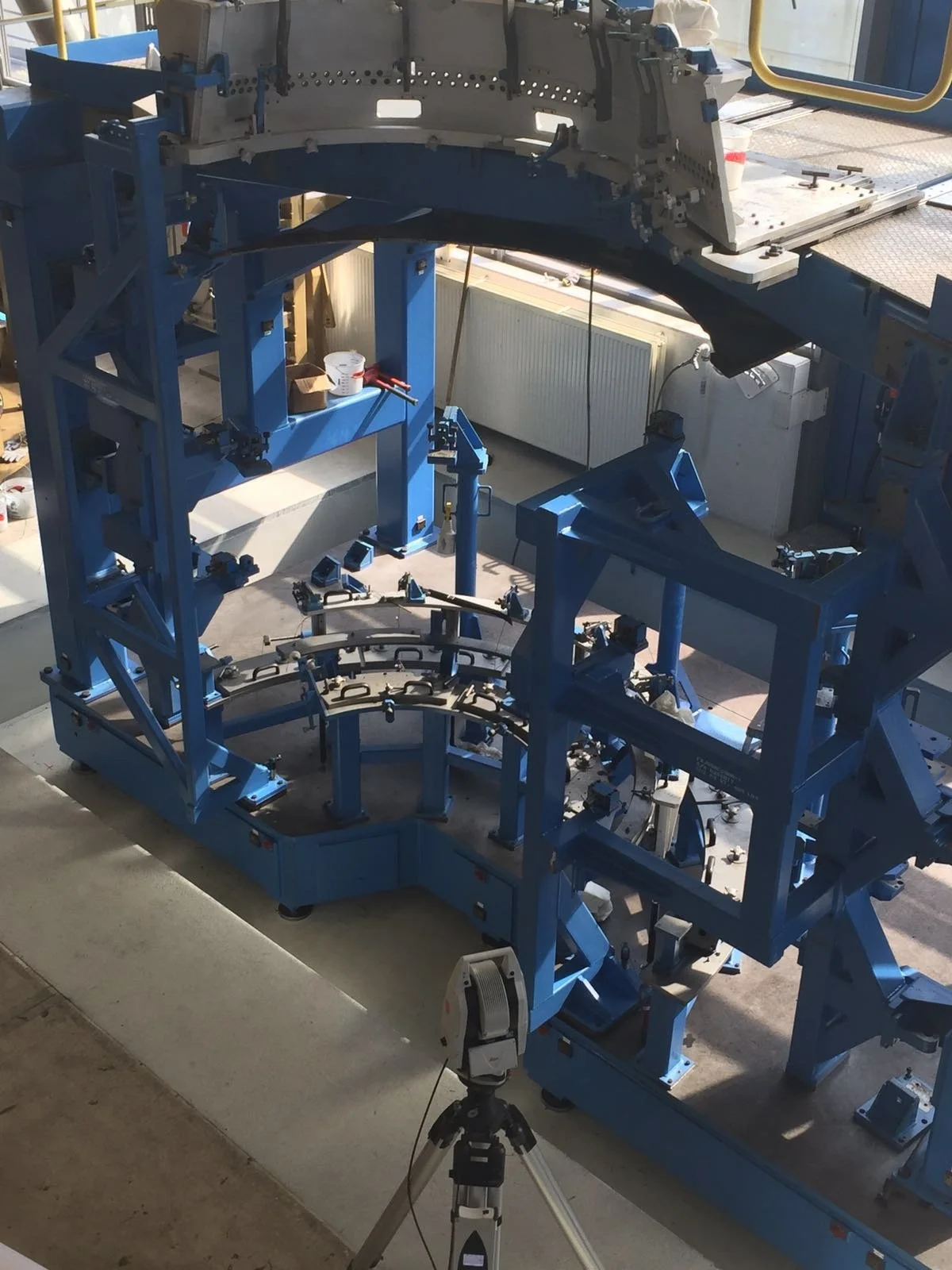
Optimising Production with Accurate Jigs and Fixture Assembly
In manufacturing, the difference between an efficient, profitable production line and one hit by delays often comes down to precision. Jigs and fixtures are essential tools in this process, holding components in place or guiding tools to ensure each part is created to exact specifications.

A Comprehensive Guide to the Benefits of Laser Scanning
Laser scanners are powerful tools in the continuously evolving field of 3D metrology. As industries strive for higher accuracy and streamlined workflows, the adoption of laser scanning technology has surged. It offers a wealth of advantages, capturing data quickly and efficiently, allowing for enhanced precision, improved speed and versatility.
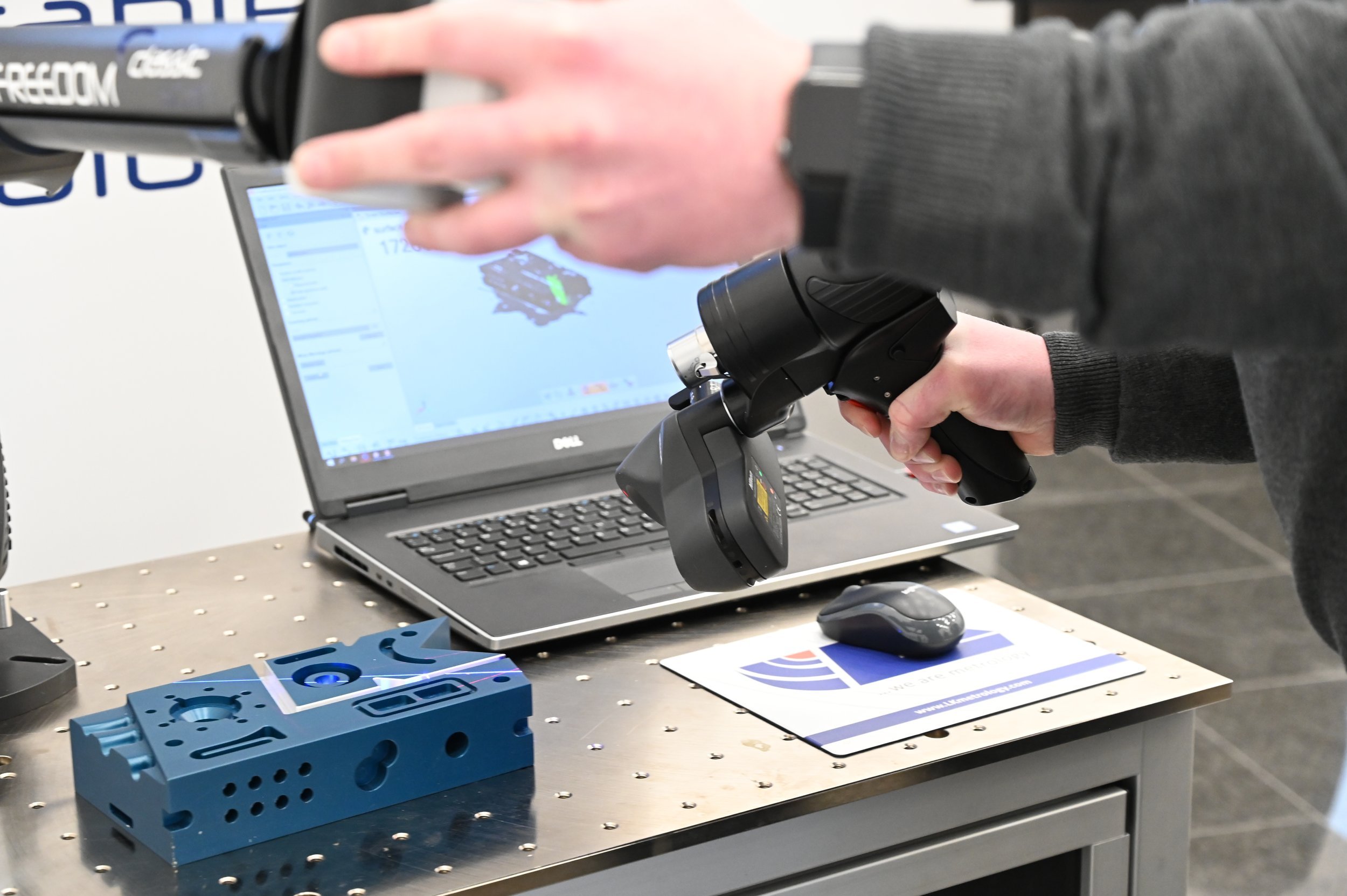
The Advantages of Portable Arm Inspection for On-Site Measurements
In today's fast-paced manufacturing and engineering environments, accurate and reliable 3D measurement solutions are critical.
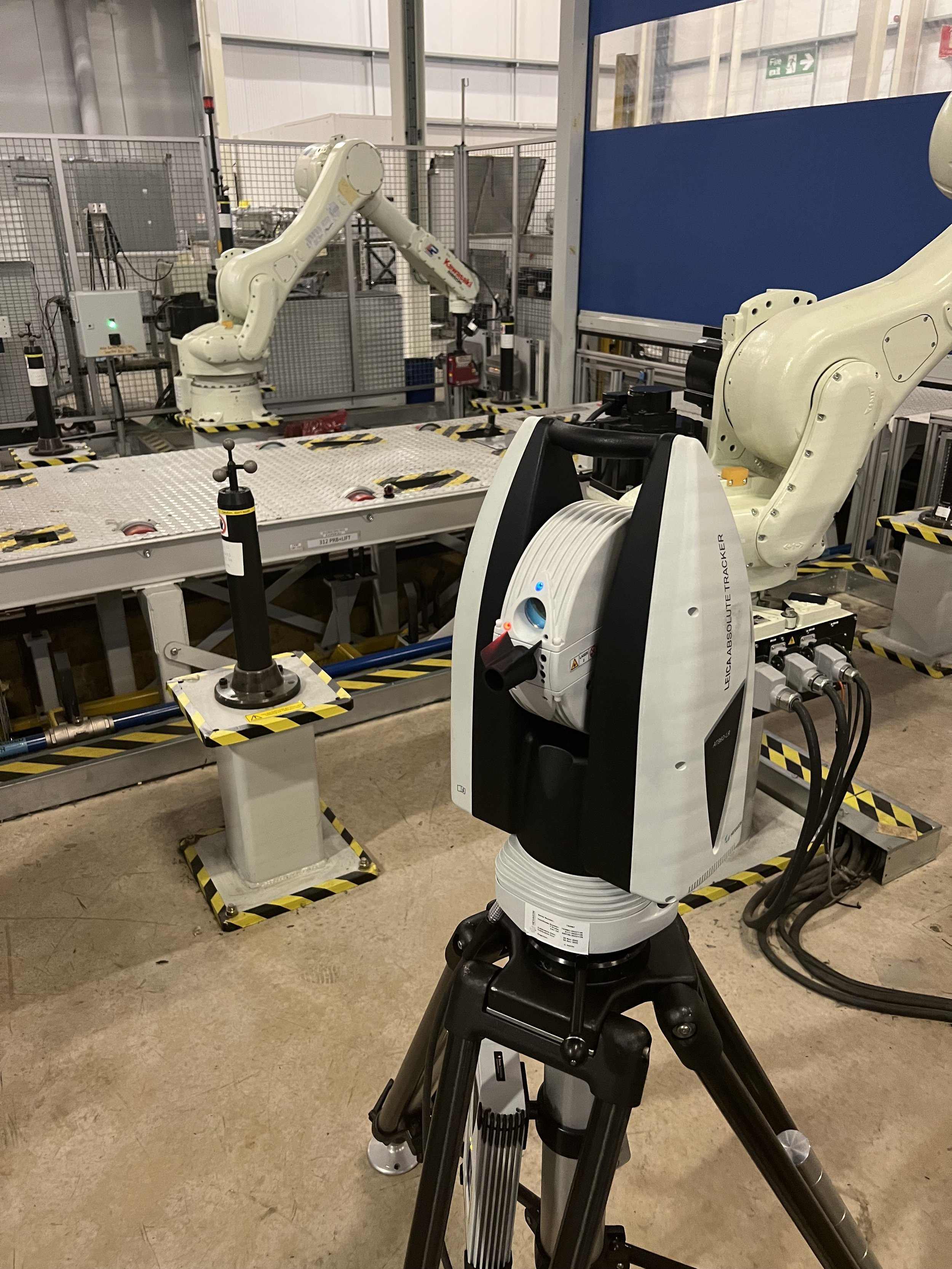
How Laser Tracker Inspection Ensures Precision in Manufacturing
Understanding the accuracy and precision of laser trackers is crucial for making informed decisions about their use in your projects. In this article, we’ll explore how laser tracker inspection ensures precision in manufacturing.